You might think that connecting the manifold and pressure testing it would be a straightforward affair – and it does most certainly appear so at first glance. Connecting the supply / return loops to the manifold is actually not so bad, you just cut the tube to length, drop a 1/2″ ProPEX ring with Stop onto the end of the tubing, and then expand the tubing using your tool of choice (I’m using a cordless Milkwaulkee ProPEX Expander Tool which is pretty slick!) – once expanded you drop in your fitting and let the tubing shrink back around it (which takes only a minute or so). From there you connect that fitting to the manifold – again, about as straightforward as it gets.
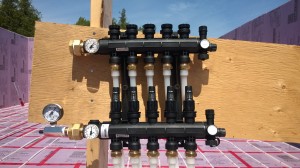
Where it gets tricky, is pressurizing the system. I ordered and received a “Pressure Test Kit” which you can see attached to the left side of the manifold in the above picture. The problem was, that this kit came as unassembled pieces, and after assembling them, it would not hold pressure. After dis-assembling, and re-assembling the kit several times, each time using progressively more aggressive pipe sealing measures, I finally got all the leaks sorted and the system seems to hold 80psi of air well for several hours.
You can also see that I re-mounted the manifold to be level before I connected all the tubing!